We’ve been designing cannabis facilities with ever increasing size. The pace was already picking up in 2017, and with the start of 2018, it launched into high gear. Among several cannabis projects, I’ve been working on a brand new 123,000 sf facility that I planned and customized for cannabis growing, packaging and distribution. The project is expected to open late 2018 and will feature three 27,000 sf tenant spaces and one 41,000 sf tenant space.
The facility was designed from the ground up to accommodate the cannabis industry; no more haphazard retrofits or hazardous or semi-legal conditions. Experienced cannabis professionals and engineers contributed to the design process, which included gathering input of experienced and successful growers. The resulting spaces offer several model units that can be customized to the client’s specific business needs. Multiple systems were considered in the design of the model units, including the structural loading for mechanical systems that support truly compliant, large scale, secure, clean and segmented production. Each unit is two stories tall with the first floor measuring 18’-0 and the second floor measuring 14’-0, with a gently peaked ceiling (free span without columns.) We include break rooms and showers in sections near the secure entries. In larger facilities, we provide separate grower and trimmer break areas that are more convenient, eliminate long walk distances, improve security, and reduce potential contamination. Two stage trimming is another configuration option for larger tenants.
We carefully considered, with legal counsel, the up to the moment status of state law, production control and tracking, levels of licenses, allowed capacity and canopy for each tenant space, and how they could convert to a consolidated approach, while in the short term keeping operations as productive as possible. We considered precedents set by Colorado, but also the direction California is going by comparison. This translates to a specific limit on the size of each tenant space and how the allowed amount of flowering canopy space is distributed in each facility. The facility is also designed so that when the state comes out with large scale artificial and mixed light licenses, we can accommodate these as well.
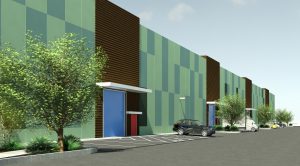
Attribution-NoDerivs CC BY ND
The entire exterior is designed with insulated metal panels that have an interior finish compliant with USDA food grade refrigeration buildings (not plywood or regular paint, which can hold contaminants and ruin crops or product packaging). Due to the better insulation, temperature control is also easier and less costly.
The facility is protected around the clock by both a team of security personnel, passive and active security along with delivery sally ports for each unit at the second layer along with secure entry vestibules key card entry minimum. All of which are discreet and professional.
Options include customized floor drainage, RO capacity, multiple air wash chambers, break rooms for both grow and trim teams, to name just a few.
We also sort through the myriad current offerings of building materials and equipment that are supposedly designed for the cannabis industry, and only use the ones that are truly tuned to our needs and not just repackaged and greenwashed with a price hike.
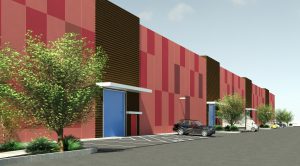
Attribution-NoDerivs CC BY ND
The facility is very flexible, and for the current trend, we have most of the spaces designed for single level HPS with RO. Most of the watering systems our clients use are very efficient and don’t typically require trench floor drains, but we allow for the option of customizing the design of the drainage for each grow room and water system.
We have also sequenced and spaced the structural system to accommodate high efficiency daylighting systems so that tenants have the choice of using more efficient mixed light growing methods. Retrofitting for the use of daylighting usually does not pencil out since the existing structural supports frequently prevent optimal spacing of the daylighting fixtures. The resulting kindness and quality from mixed lighting cultivation is rather controversial still, but as the technology improves, we’ll further integrate it into our designs.
To find out more about the production flow design for both double HPS and LED, security, high capacity electrical systems, and many more proprietary details, contact Brant Fetter at 510-231-7509 or Andrew Butt at 510-231-7507